Application
Variables for Powder Coating Systems
Ken
Kreeger
Powder Systems Group
Nordson Corporation
Introduction
Despite the effect of several years of worldwide economic slowdown,
the powder coating industry continues to grow in North America with
an average annual rate (in pounds produced) of 12 to 15 percent.
This rapid growth of powder coating has put a strong demand on equipment
suppliers to develop more efficient ways of applying powder coating.
The purpose of this article is to provide an overview of powder
application technology and variables that affect first-pass transfer
efficiency.
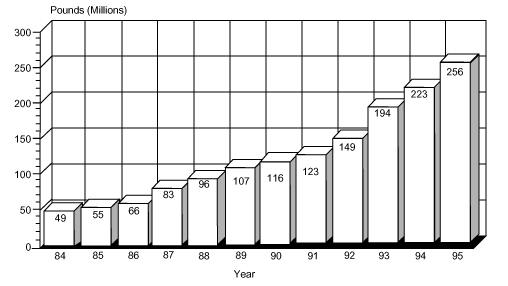 |
North
American Thermoset Powder Coatings Production |
Powder
Coating Principle of Operation
The electrostatic application of powder coating to a part begins
with fluidization. Fluidization is a process where powder being
sprayed mixes with compressed air, enabling it to be pumped from
a container and supplied to the spray guns. The powder flow is regulated
by controlling
the air supplied to the pump. The powder supplied to the spray gun
is charged using either a corona or tribocharging gun. Charged powder
moves to the grounded workpiece with the help of air supplied to
the guns and the airflow in the booth.
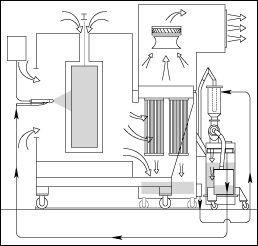 |
Figure
1:
Flow Schematic |
When
the powder particles come close to the part, an electrostatic attraction
between the charged powder particles and the grounded part adheres
powder to the part. The coated part then passes through an oven
and is cured. The oversprayed powder is contained within an enclosure
and drawn into the primary filter cartridges by a centrifugal fan.
Circulating air, now free of powder, is discharged through high-efficiency
final filters into the plant as clean air. The primary filter cartridges
are periodically reverse-pulsed to remove oversprayed powder. The
powder is then sieved and supplied back to the guns to provide extremely
efficient material for use again. A simple diagram showing how this
process works is shown in Figure 1.
Application
Transfer Efficiency
What is first-pass transfer efficiency? It is defined as the amount
of powder applied to the part compared to the total amount of powder
sprayed by the application equipment. There are many variables to
consider in achieving first-pass transfer efficiency. These variables
and the applications that can affect first-pass transfer efficiency
are discussed in the following pages of this paper (Figure
2).
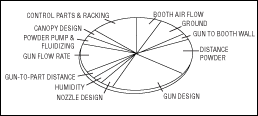 |
Figure
2:
Application Transfer Efficiency Variables
|
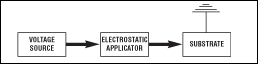 |
Figure
3
|
Gun
Design / Nozzle Design
Corona and tribo charging are two methods widely used in commercial
electrostatic powder spray equipment. The most popular method used
in North America today is the electrostatic spray process which
is comprised of three main components (Figure 3).
Electrostatic
Powder Spray Guns
Functions of the electrostatic powder spray gun are to:
- Shape
and direct the flow of powder.
- Control
the pattern size, shape and density of powder.
- Impart
the electrostatic charge to the powder being sprayed.
- Control
the deposition of powder onto the parts being sprayed.
Charging
System
The purpose of the charging system is to create a force within the
sprayed powder particles enabling them to cling or attach themselves
to bare, grounded metal parts as shown in Figure
4.
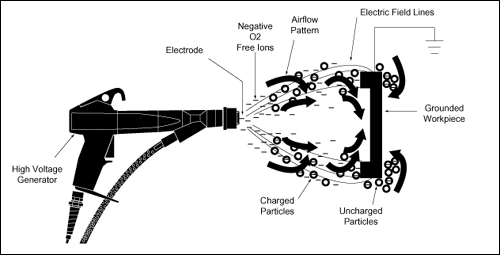 |
Figure
4: Corona
Charging Powder Gun
|
Electrostatic
Corona
High voltage or low voltage cables are the two basic ways that the
voltage source is currently applied to the tip of a corona-charged
powder spray gun. The type of cable depends on whether the high
voltage generator is an external or internal power supply gun. Both
come in negative or positive polarity. Generally, corona charging
uses a negative polarity on the electrode as negative polarity produces
more ions and is less prone to arcing than positive polarity. The
charging electrode is held at a very high negative potential, requiring
a power supply rated from 30,000 to 100,000 volts. Positive polarity
guns are used when spraying nylon or touch up in an automatic tribo
system. Figure 5 illustrates an external power
supply gun and internal power supply gun for voltage generation.
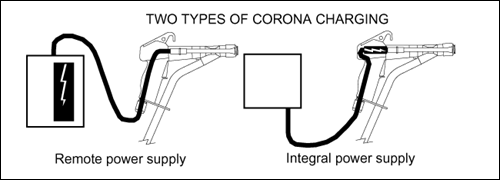 |
Figure
5: Corona
Charging Methods
|
Corona
Design Criteria
- Charge
in a region of high field strength.
- Charge
where air velocities are low.
- Charge
where the powder is well dispersed.
- Arrange
the geometry of the charging electrode so the ions flow through
the powder stream and the electrode is in the direct line of sight
of the ground.
The
above design features should be consolidated with the pattern of
powder flow, equipment cost(s), ease of maintenance, and durability.
Tribo
Charging
The word tribo is derived from the Greek word tribune, meaning to
rub or produce friction. In tribo charging, the powder particles
are charged by causing them to rub at a high velocity on a surface
and thereby, transferring the charge (Figure 6).
Without an external power supply and a charging field in front of
the gun, tribo charging virtually eliminates the problem of faraday
cage effect. The powder particles take on a positive charge
inside the gun due to the loss of electrons. The particles are now
free to be directed to where they are needed. The powder flows into
recessed and difficult-to-reach areas by nozzle direction and air
flow. Because the particles are charged in the gun and there are
no lines of force, it is less likely that the powder particles will
build up on the leading edge of the part being coated. The advantage
to this is the near elimination of fatty edges resulting
in a uniform coating and even film build on the product.
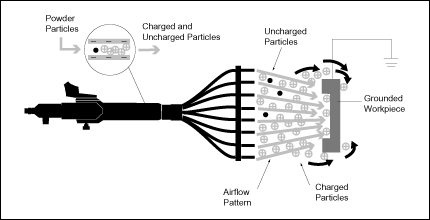 |
Figure
6: Tribo
Charging Powder Gun
|
One
thing to note, tribo charging is much more dependent on correct
powder formulation (chemically) and particle grind size than corona-charging
equipment. It is imperative that all powders be tested in tribo
equipment to ensure good results.
Powder
Spray Guns
The two major gun categories are manual and automatic. Manual guns
can be used in stand-alone units, applications not requiring automatic
guns, or with automatic systems that are generally used for difficult-to-reach
and/or complex parts.
Since
the hand painter uses the spray gun for long periods of time, the
flexibility, weight, efficiency and durability of the spray gun
are important. When considering the added mass of the hose and cable,
keep in mind that most painters will hold the hose and cable with
the other hand so that only three or four feet of hose and cable
weight are added to the gun. Also, depending on where the hose and
cable are attached to the gun, the added weight may improve or degrade
the overall balance. (Note: Work with your equipment supplier to
help determine the right nozzle type for your application.)
Automatic
guns may be fixed, on gun movers, or a combination of both. In many
cases, systems may be totally automatic without handguns for touch
up. Remote power supply Integral power supply
Here
are six things to consider before you purchase your next powder
gun:
- Is
the gun easy to disassemble and reassemble?
- Is
there a variety of nozzles?
- Ease
of cleaning for color change?
- How
many wear parts?
- Where
is the manufacturing facility?
- Test
the gun on your parts.
Each
type of gun has its place in the market depending on the application.
The justification for each has to do with its specific design and
overall chargeability. The most important thing to remember is the
powder gun is just one piece of the application pie.
Nozzle
Design
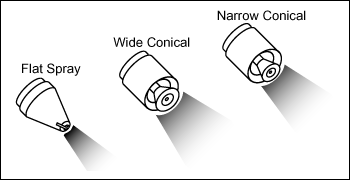 |
Figure
7: Nozzle
Selection
|
The
gun and nozzle design is a major influence in achieving first-pass
transfer efficiency. As previously discussed, charge where air velocities
are low and where the powder is well dispersed. This is where the
nozzle design comes into place. The two most widely used nozzles
are the deflector-pattern nozzles and flat spray nozzles. Both are
available in various pattern shapes. The flat spray nozzle is more
directional and has a well-defined pattern. The deflector-pattern
nozzle has a soft, well-dispersed pattern and has the appearance
of a liquid bell. There are many other nozzle types, but these account
for 90 percent of the usage in todays powder coating systems.
There are gun extensions that will help you reach deep recessed
parts safely and without too much effort (Figure
7).
Powder
Pump and Fluidizing Gun Flow Rate
The purpose of the pump is to supply powder to the gun at a uniform
and consistent rate. Powder pumps use a venturi principle to deliver
powder from a supply hopper to the powder spray gun. The lowest
flow rate possible is the ideal condition for first-pass transfer
efficiency while still maintaining coverage through each gun. Consistent
with the theory of high-charging efficiency is control of the powder
output of the guns. The more powder passing by the gun electrode,
the less chance each particle has in picking up the maximum charge.
More powder flow is not better when dealing with transfer efficiency.
It is better to add additional powder guns to keep outputs low than
to reduce the number of guns and increase the output per gun.
A fluidizing
hopper/feeder with level control is probably the most overlooked
and underrated device of any powder system. Lets look at some
of the critical design criteria of a fluidizing hopper:
- Level
control.
- Fluidizing
plenum.
- Venting.
A good
level control will enable the fluidizing feeder to maintain a consistent
powder height and a consistent feed rate.
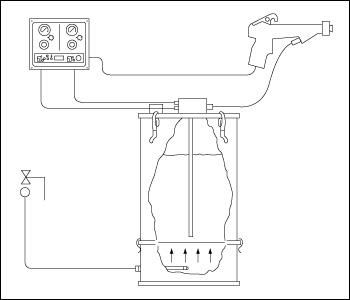 |
Figure
8: Powder
Feed Hopper
|
The
fluidizing plenum is designed to distribute the air uniformly across
the fluidizing membrane which in turn provides uniform fluidization
throughout the interior of the feed hopper. More fluidizing air
flow is not better when dealing with transfer efficiency. Too much
air or nonuniform distribution of that air will result in extremely
violent fluidization in certain areas. As a result, efficiency of
the powder pump will be reduced causing the powder pump to draw
air and reduce the powder flow rate.
A powder
feed hopper is like a pressure vessel in some ways. The feed hopper
receives powder through three to four venturi transfer pumps. These
pumps are basic and air-type pumps, and the air pressure from the
pumps and the fluidizing bed has to be relieved from the hopper
feeder. Thebest way to remove the excess air is through a direct
vent design. This design relieves internal pressure back to the
collector as shown in Figure 8.
Controls
/ Parts and Racking
Process control and monitoring devices can enhance the operating
efficiency of your powder coating system. When you look at first-pass
transfer efficiency, consider a system where the guns are triggered
on at all times and the space between the parts is equal to the
part size. The highest achievable first-pass transfer efficiency
of your system will be no more than 50 percent because one-half
of the powder is sprayed into the air. Using a stop watch, record
the amount of time the guns are spraying without parts in front
of the gun. System history has shown us that the time will vary
from 20 to 60 percent of the time the guns are spraying with known
parts in front of the guns.
Your
overall first-pass transfer efficiency could improve from 20 to
60 percent based on gun triggering. An added benefit of automated
gun triggering is the ability to adjust the spray duration to either
reduce heavy edges on parts or to increase wrap on parts (Figure
9).
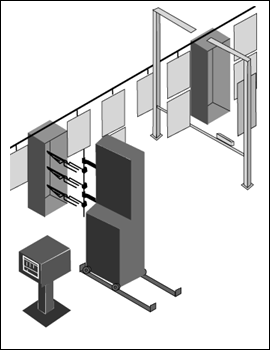 |
Figure
9: Automatic
Gun Triggers
|
Booth
Air Flow
Uniformity in the booth air flow is one key piece of the application
variables chart. Previously we discussed that more powder
flow is not better when dealing with transfer efficiency.
More air flow will also affect your first-pass transfer
efficiency. As this section of the paper deals with application
transfer efficiency variables, powder booths are designed with two
requirements; 1) powder containment and 2) safety. We will focus
on powder containment.
The
first requirement in any powder system is powder containment. To
contain oversprayed powder particles, the powder booth is designed
to provide average face velocity of 100 lineal feet per minute (lfpm)
air flow across all openings.
Following
are some exceptions:
- Tall
parts greater than 6'0".
- Heated
parts greater than 1200 F.
- Crossdrafts
in excess of 60 FPM in area of the booth.
- Short
hooks up to 18".
Again,
we are looking for powder containment. Too much air flow will draw
the powder away from the parts being coated. Many try to overcompensate
with a higher powder flow rate and less first-pass transfer efficiency.
Booth
Canopy Design
The design of a powder coating booth begins with the canopy or enclosure
that contains the oversprayed powder. The canopy is best described
as a small room with four walls, a floor and a ceiling. The ceiling
has a slot running lengthwise through which hangers from the conveyor
protrude to support the part to be coated. Because powder is applied
via an electrostatic charge and our goal is high first-pass transfer
efficiency, we want the powder to be attracted to the part and not
to the booth. To achieve this, the booth canopy or the area around
the automatic powder guns should be constructed of a low, non-conductive
material. This will allow the electrostatic field emitted by the
guns to attract the powder to the part and not the booth wall.
- Gun-to-Booth
Wall Distance
One canopy issue that will affect first-pass transfer efficiency
and good housekeeping is the distance of the tip of the gun to
the booth canopy behind the gun. The powder gun should be at least
12 inches inside the booth so the electrostatic field is attracted
to the part and not to the booth canopy. If the base of the powder
booth is not wide enough to place the gun inside the booth, you
can add a booth wall extender at the gun opening for added space
between the gun tip and the wall. As a result, more powder is
attracted to the part, increasing operating efficiency. This also
speeds up booth cleaning during color changes.
- Gun-to-Part
Distance
The distance between the parts you are coating and the tip of
the gun will affect your transfer efficiency. There are many variables
with gun placement that depend on line speed and part specification.
Generally, start at 8 to 12 inches away from the part.
Humidity
Both humidity and temperature can affect the performance of a powder
coating system. The powder system should be installed in an environmental
room. The value of an environmental room is consistency as any change
in temperature and humidity may affect fluidization, filter efficiency,
filter life, and charging capabilities of the powder. Temperature
of the environmental room should remain at 680 F to 800 F. Relative
humidity should remain at 47 to 55 percent.
Ground
Part grounding is extremely important. An ungrounded substrate will
attract the charged powder to a certain point. After which, it begins
to repel the charged material. It will also affect your first-pass
transfer efficiency. An ungrounded part has the potential to ignite
the powder and create a fire.
Ground
is measured as one megohm resistance.
Powder
There are physical and chemical properties that can affect first-pass
transfer efficiency. Not all powders are the same, so I would recommend
you work with your powder supplier.
Summary
In the past decade, powder coatings have come a long way. The full
potential in North America remains to be realized. The value of
first-pass transfer efficiency is important, but lets not
fool ourselves. First-pass transfer efficiency is more than a powder
gun. Its a totally integrated system. In some cases, a piecemeal
system may look like a powder coating system but the overall performance,
operating cost, quality and system efficiency fall short of a totally
integrated powder coating system.
Future
developments in the powder coating equipment industry will focus
on first-pass transfer efficiency. It could be economically feasible
to spray-to-waste by increasing the transfer efficiency of the application
equipment. As a result, we would achieve a faster color change equal
to that of a liquid paint system.
Serving
the Finishing Industries. Since 1936.
PF Onine and all contents are properties of Gardner Publications,
Inc.
All Rights Reserved.
|